电池制造 | 万可自动化解决方案打造面向未来的能源
2024-2-23新闻
科技驱动能源转型,新能源市场一直保持着高速发展。在汽车行业向碳中和运输方向转变时,可再生能源电池存储系统和便携式电子设备变得越来越重要。万可丰富的自动化控制和工业接口模块产品可为电池制造设备提供理想的自动化解决方案。

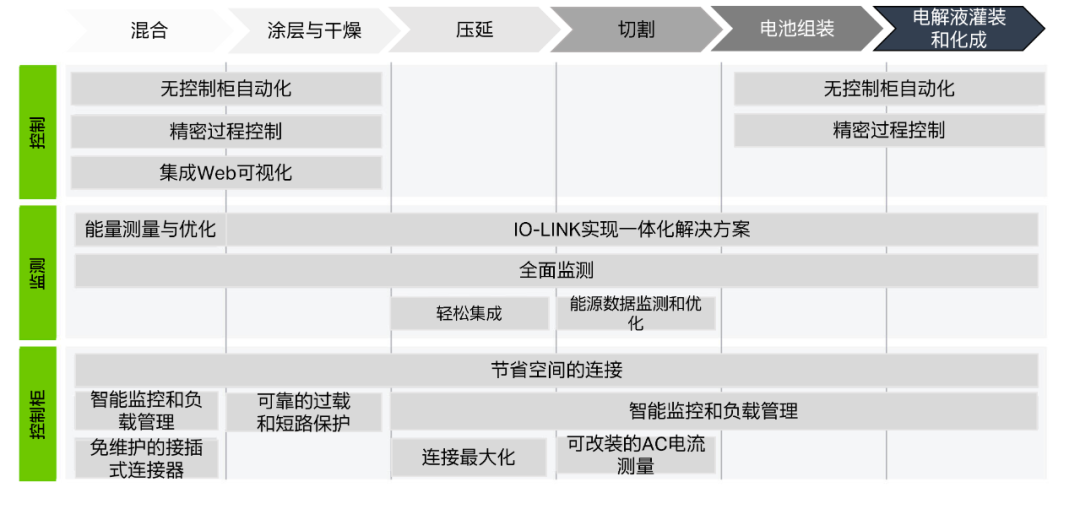
电池的制造从浆料制备开始。由正极配方和负极配方组成的两种单独的原料组合形成浆料。制备过程中需要使用导电添加剂、溶剂和粘结剂。温度在其中起着决定性作用。
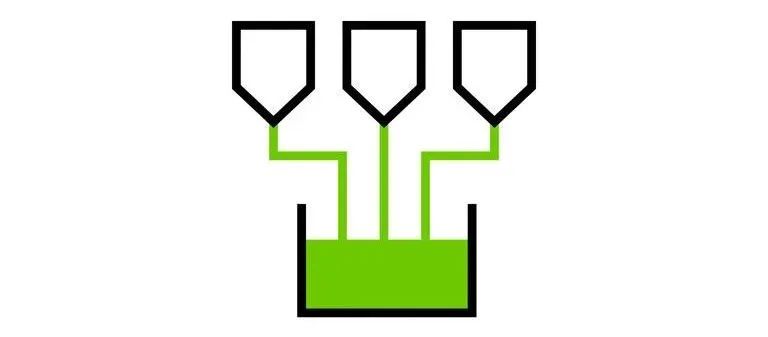
万可I/O System Field控制器和万可PFC200控制器能控制液体的温度,液体温度必须在20到40摄氏度之间。此外,万可MID电能表可监控能源消耗。由于整个过程都在洁净室中进行,浆料通过管道或大气密封的储罐进一步运输到随后的“涂层”过程步骤。
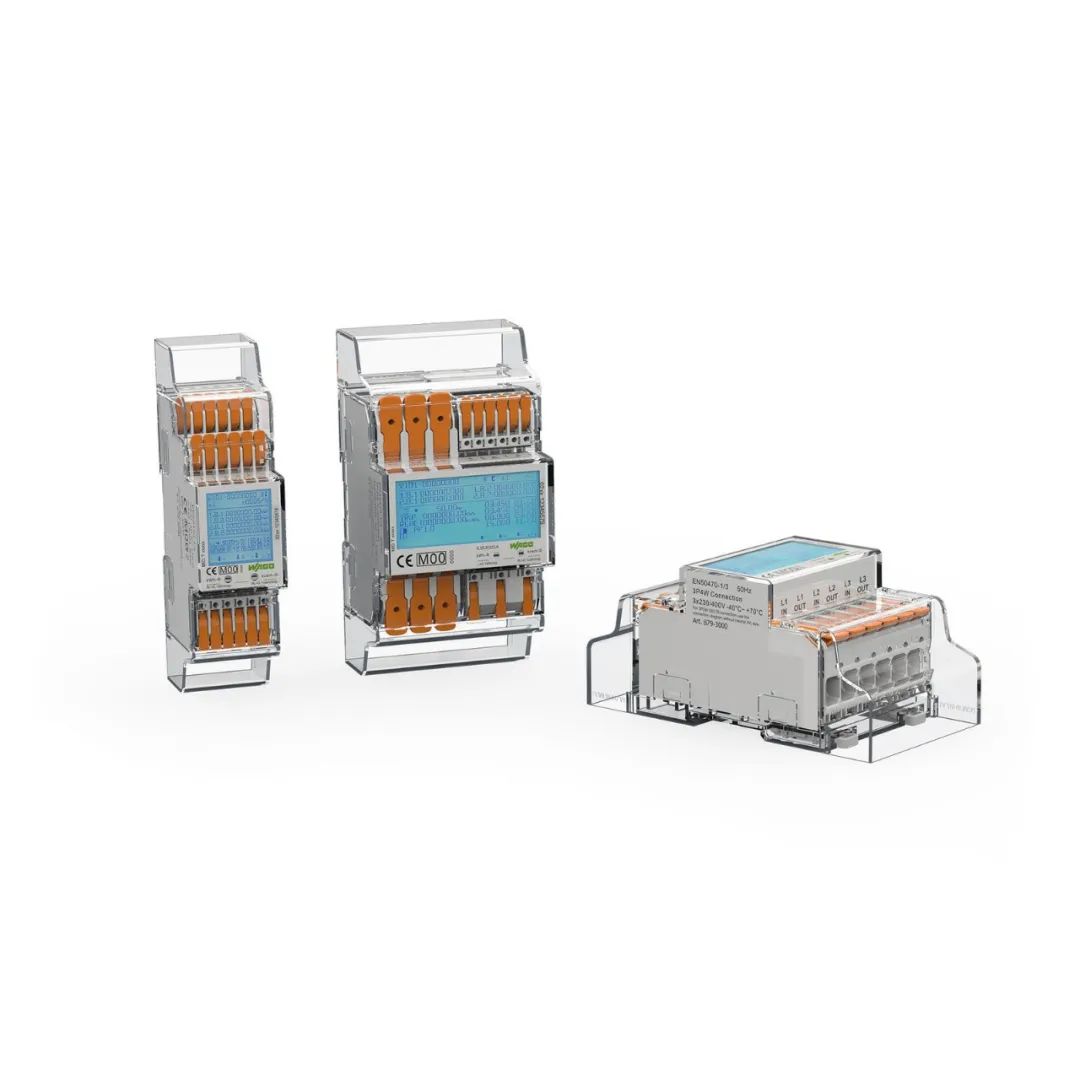
万可MID电能表
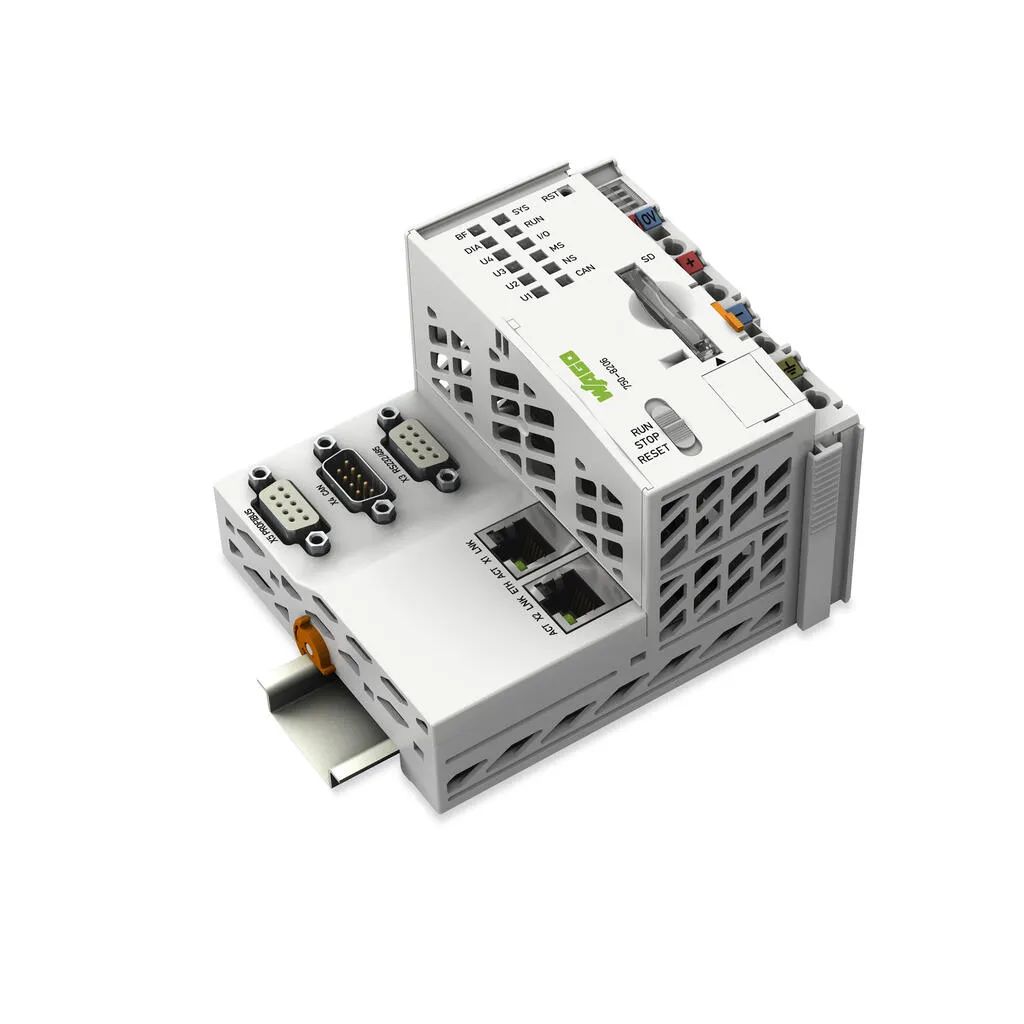
万可PFC200控制器
在涂层过程中,使用涂抹工具用滑片涂覆载体箔以制备膜。这种载体箔由铝箔或铜箔等材料组成。根据电池设计,层厚度为10μm至25μm不等。
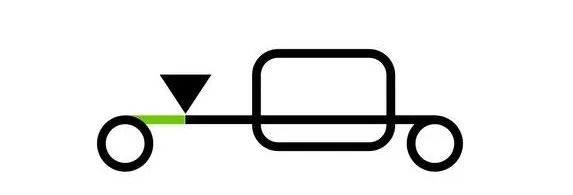
根据系统,可依次或同时涂覆箔的顶侧和底侧。万可I/O System Field和万可I/O System 750系统是监控层厚度的理想之选,有助于在电池制造过程中保持高品质标准。
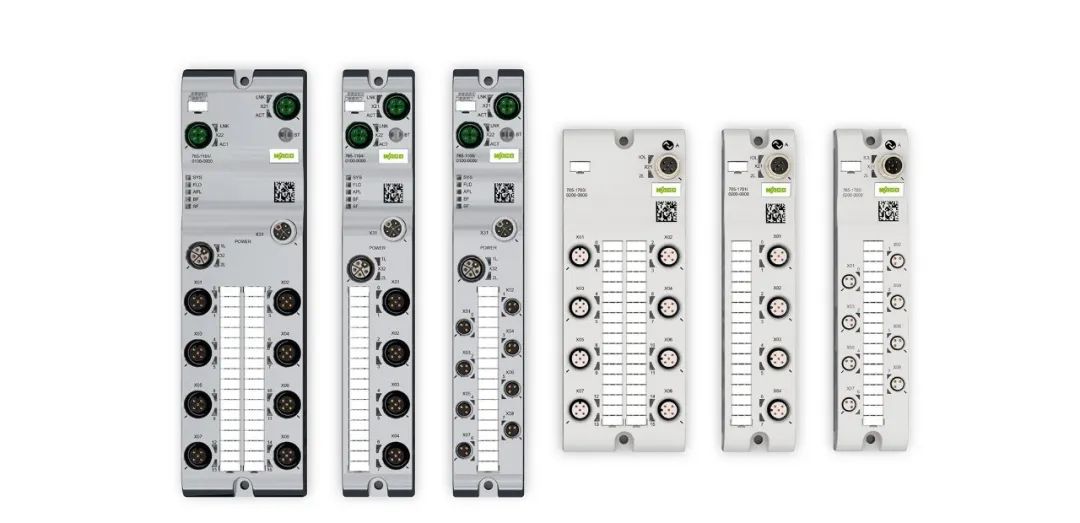
万可I/O System Field
一旦涂覆过程完成,则进行干燥。将铝箔或铜箔送入干燥器。这种浮式干燥器用于在两侧同时实施涂覆。干燥器长度对生产速度至关重要。干燥器划分为不同的温度区,以实现单独的温度分布。万可I/O System Field与万可PFC200相结合,是精确地维护和监控温度的理想解决方案。
压延过程也称为轧制,是指使用一对或多对旋转的轧辊来压紧双侧涂覆的铜箔或铝箔。上辊和下辊将箔片压紧。线压决定了涂层基体的孔隙率。如果线压设置得过高,则会导致基体材料被压碎或损坏。轧制过程旨在补偿极其细微的不规则性。
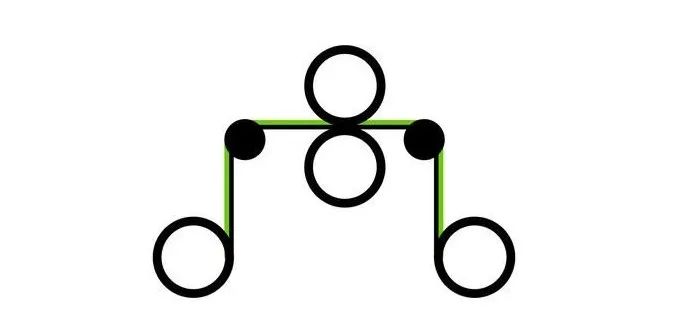
由于坚稳耐用,万可I/O System Field和万可I/O System 750也非常适用于监控轧制过程。
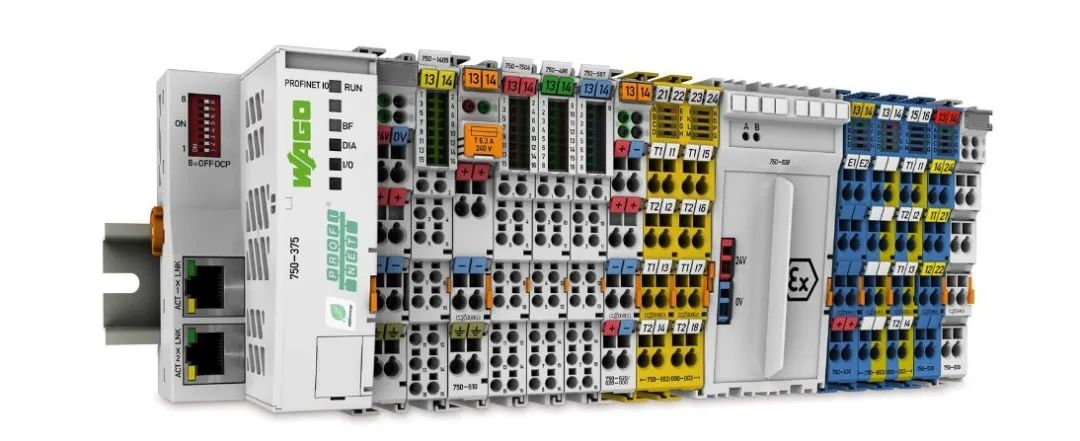
万可I/O System 750系统

切割是将较宽的电极条(母线圈)分成几个较小的条(子线圈)的分割过程。切割可以是热切割(激光切割)或机械切割(使用滚刀切割)。电极条的清洁性至关重要,因为杂质或残余物会损害子线圈的质量,并最终影响电池性能。通过抽吸和/或使用刷子清洁电极条,以确保生产过程中的顺利运行和质量保证。子线圈的切割宽度取决于电池设计,在许多应用中在100mm和300mm之间。

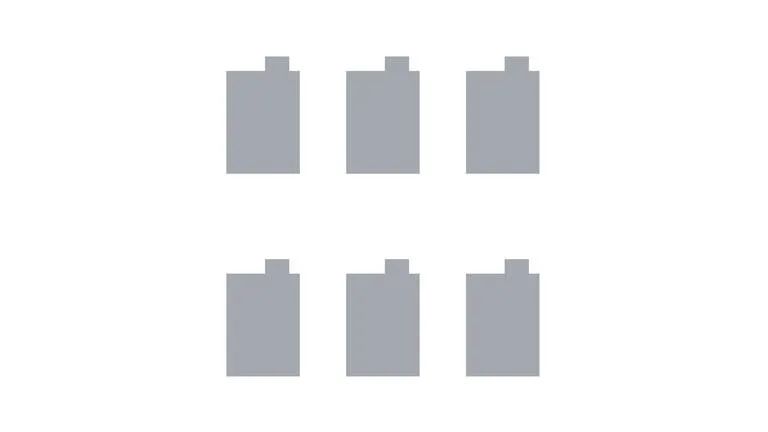
万可Pro 2系列电源具有独特的通信接口,可单独监控和评估生产过程,并尽可能高效地配置电池制造过程,从而降低生产成本。
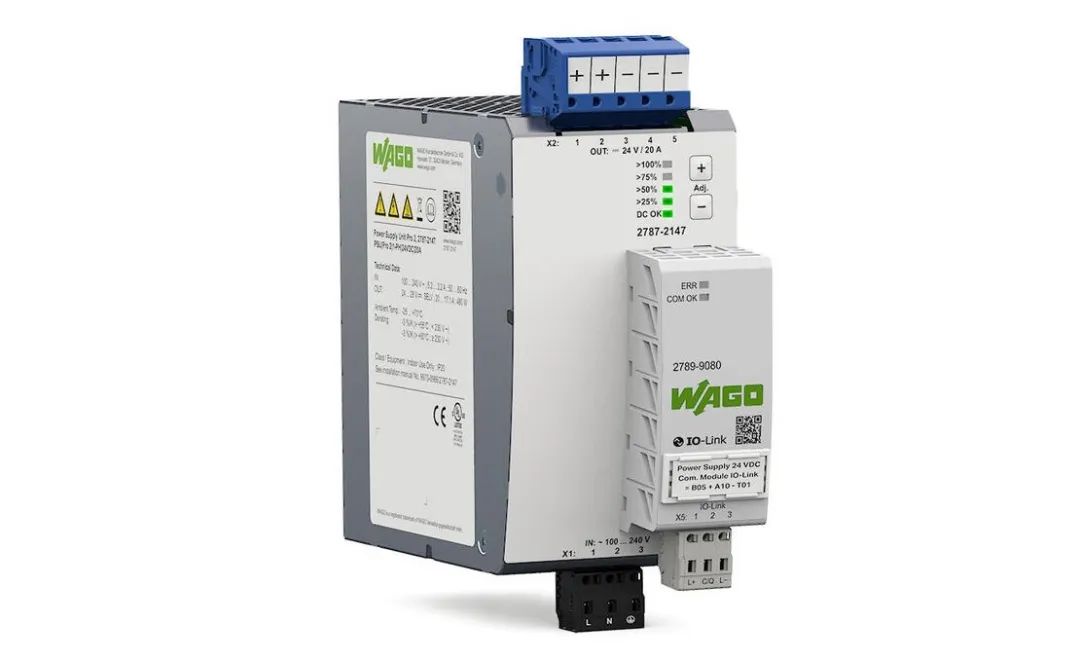
万可Pro 2电源
以上切割过程是生产软包电池封装的必需步骤。
堆叠好的电芯需经过极耳焊接,将焊接好的电芯放置于冲坑后的铝塑膜中并进行顶、侧封等工序,形成未注液的软包电池。而将同组别的单体电池按照一定的串并联方式组装,就可以应用于电动汽车、储能等领域。
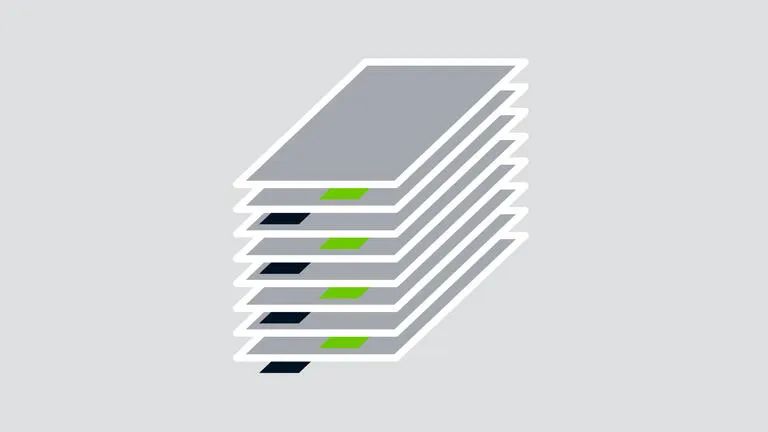
I/O System Field与IO-Link结合使用,可充分发挥其作为灵活“IO分配器”的优势,有效用于数据收集和分配。该通信标准支持从控制级到传感器和执行器层面的无缝数据流。这可大大简化配置和布线流程。同时还为诊断、参数化和设备识别提供了全新的可能性。
电解液灌装是电池制造的最后一步,在将电池组放入封装后进行。开口通过密封方法或使用带有焊接封闭盖的芯轴插入件进行密封。在圆形和棱柱形电池中,执行预老化以防止由于气体形成而引起变形。
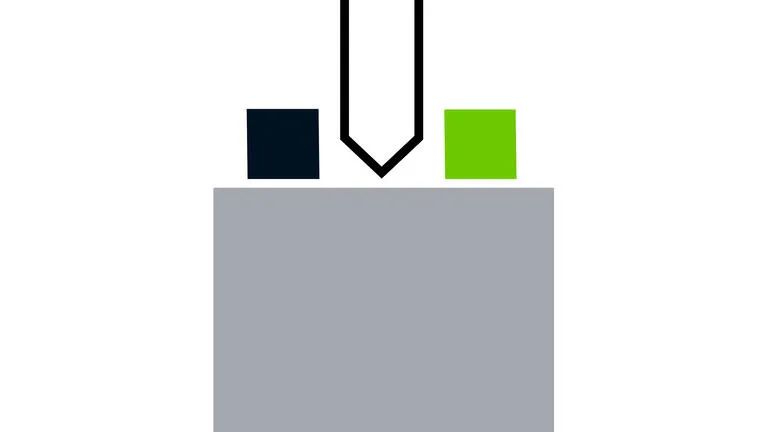
万可Pro 2开关稳压电源可满足多种供电需求,其负载管理可彰显智能化特性,能可靠地为电池制造设备供电,同时对其进行保护。
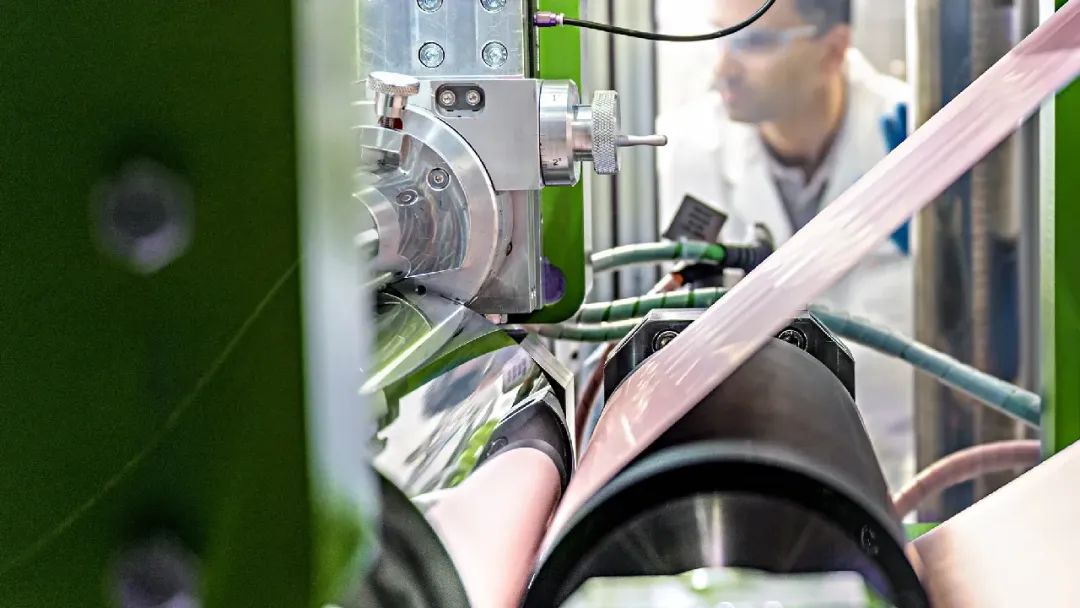
推动电池制造向智能化、绿色化方向发展需要一套成熟的自动化解决方案助力电池制造装备生产效率和产品质量的提升。万可自动化解决方案可以协助客户一起打造面向未来的新能源时代。
免责声明:本文转自网络,版权归原作者所有,如涉及作品版权问题,请及时与我们联系删除,谢谢!

End.
想了解更多产品信息、行业资讯
↓
新浪微博 - 视频号 - 官网
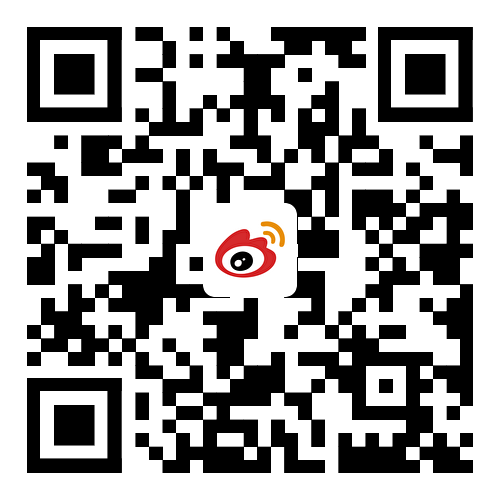
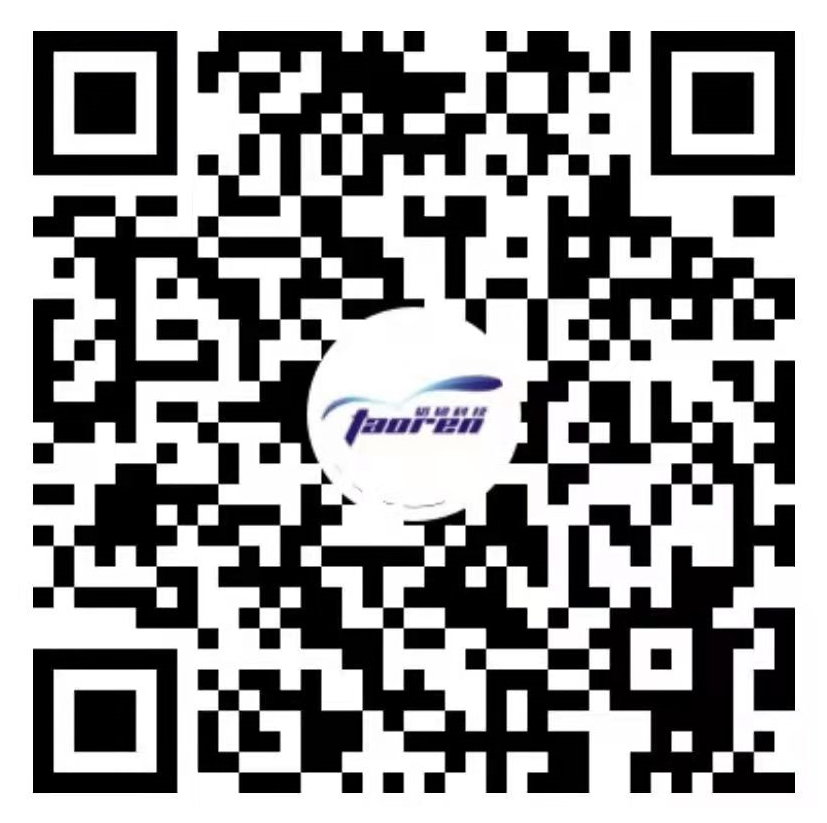
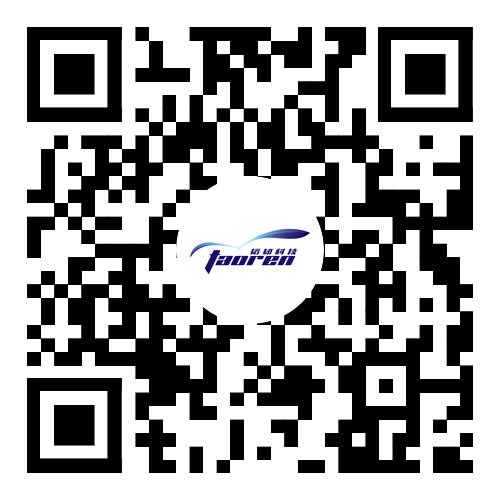
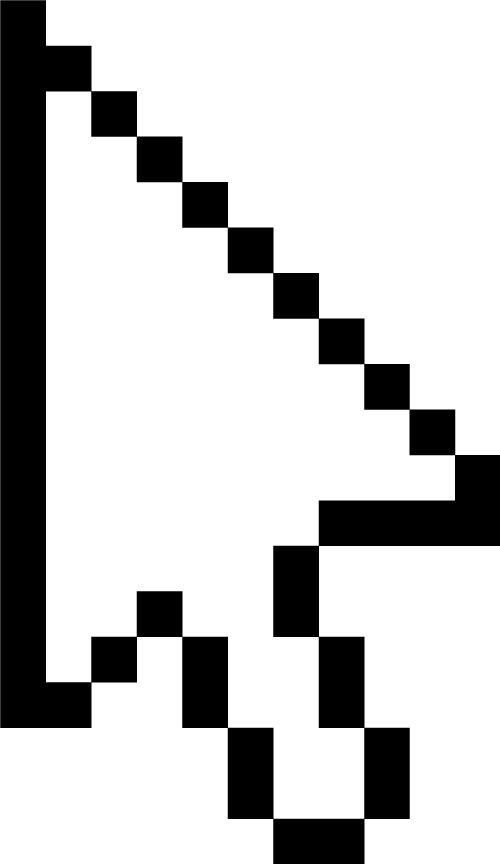
分享、在看与点赞
只要你点我都喜欢
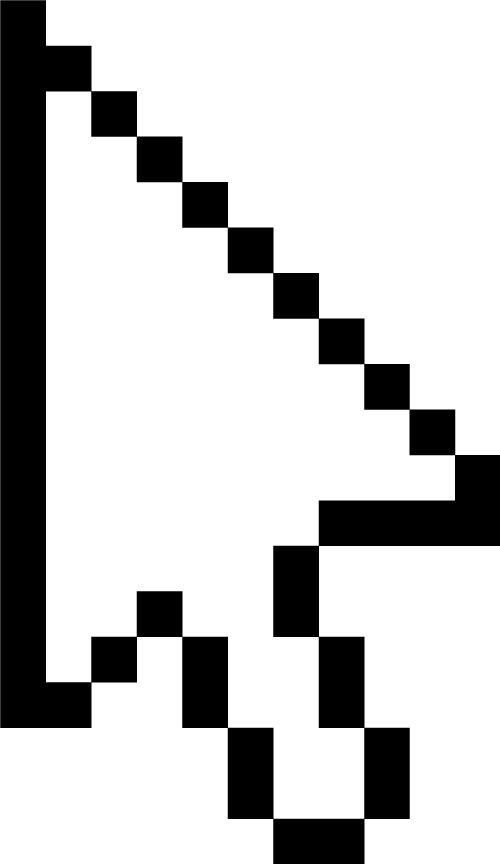